MGA Thermal
Demonstration Unit
Proven ability to charge, store and discharge to design specifications at scale.
Supported by ARENA and Shell Gamechanger.
About
MGA Thermal has received AUD 1.26 million in funding from the Australian Renewable Energy Agency (ARENA) for our MGA Thermal Energy Storage Project.
Using our proprietary Miscibility Gap Alloy (MGA) technology, the project involves the design, manufacture, and operation of a 5 MWh demonstration-scale thermal energy storage (TES) system.
Supported by energy giant Shell, and partnered with Varley Group this project includes building and demonstrating the performance of our MGA TES technology under testing scenarios that simulate a variety of end-use applications. The cases include providing dispatchable power, process heat, and green hydrogen production. The project will produce data and insights to inform business cases for future applications of the technology.
Key Specifications
5 MWh
500 kW nameplate thermal power
Discharge steam 200C, 7 bar, for 24 hours
Approx. 3700 MGA Blocks
12m L x 3m W x 4m H
Impact
The project is a major milestone for MGA Thermal, it will:
validate the technical performance of MGA Thermal’s proprietary TES technology under a variety of end-use case simulations
improve understanding of the techno-economic business case for MGA Thermal’s technology in comparison to competing energy storage technologies
demonstrate the potential role that TES technology could play in the Australian energy market including for dispatchable electricity and process heat.
MGA Thermal has many applications of MGA thermal energy storage material, we work with customers to find energy storage solutions that best work for their requirements - Learn more about MGA applications.
Market
The global shift to decarbonisation is driving a swift uptake of renewable energy generation. Renewable energy, such as wind and solar is intermittent and often doesn’t align with market demand requirements. The Australian Energy Market Operator’s 2022 Integrated System Plan urges significant investment in new flexible, dispatchable capacity to support growth in renewable energy as the thermal fleet retires.
Background
MGA Thermal’s TES system was developed after nearly a decade of research and development at the University of Newcastle. After founding in 2019, the company has quickly scaled to be a competitive solution for global energy market decarbonisation. MGA technology has the potential to be a cost-effective medium-duration storage technology thanks to its unique design with high energy density, low energy degradation, modular blocks, and low-cost materials.
As part of our ARENA project, we are providing up-to-date information on the progress of our Demonstration Unit. We update this section regularly to include project milestones in each month.
Recent Developments
-
In August, the demonstration plant project and ARENA’s support announced by Hon Chris Bowen MP and Ms Meryl Swanson MP on 10 August 2022. Core process equipment began arriving on-site at Tomago, NSW.
By September: Varley Group had started the manufacture of the TES module design and core process equipment continued to arrive on-site at Tomago, NSW.
During October, Varley Group was finalising the enclosure fabrication – putting the finishing touches on the weldment to make it gas-tight. The detailed drafting of the ducting and piping layout has been completed and material procurement has begun. All core process equipment arrived on site ready for the arrival of the enclosure.
In November 2022, the demonstration plant was on track for commissioning in 2023 with all major process components including the steam generators, pumps, electrical components, and valves now on site. We had also taken delivery of the thermal energy storage (TES) enclosure from Varley Group, which was an exciting tangible step in the project delivery as the structure forms the main part of the thermal energy storage; the assembly phase is underway!
The December shared more on timelines; Following the arrival of the TES enclosure from Varley, the insulation, ductwork, piping, and other assembly activities will take place over the next 8 weeks, followed closely by the installation of MGA Blocks and heater elements ready for commissioning to begin.
-
January – Assembly began! In December, the TES enclosure arrived from Varley and since then we had installed the insulation, and supporting infrastructure such as cable trays, supports, and pipe/duct supports were placed and mounted. We also began installing the instrument cables. Our representatives travelled to Brisbane to attend the Factory Acceptance Test for the switchboard, which was fully tested to meet the acceptance criteria.
February – Assembly continued… The gas circulation system had been installed, including the fan, 3-stage steam generator, ducting, and valves. The instrument and power cables for the heating and temperature measurement system were completed, and these were routed to the switchboard which was safely received and installed on-site in early February. Commissioning was fast approaching; the plans were being finalised and pre-commissioning check sheets were being carried out.
Excitingly, in February 2023, we also announced that MGA Thermal received funding from energy giant Shell to support the completion of this demonstration unit.
March – All major construction items were on-site, and we continued to piece them together. We completed a simulated site acceptance test of the control software with our engineering partners, stepping through each control step to ensure the logic was correct. The water treatment plant, which would provide quality water to our boiler and cooling systems (to ensure minimal corrosion and damage to our equipment) was also finalised with installation to begin shortly. Looking forward, we engaged an experienced Commissioning Manager to begin developing the appropriate procedures to transition the plant safely and effectively from construction, through commissioning, to operations.
April – Construction of the high-pressure steam piping, the last portion of the plant to be installed, had begun! Careful control of the installation of this part of the plant was crucial to meet regulatory and safety requirements, ensuring the risk of failure during operation was mitigated. The site was a buzz of activity, with hundreds of meters of pipes being laid to service the water treatment plant, cooling water, and steam systems. As construction items came online and instruments and equipment were installed, the electricians were also able to progress by laying cable and terminating to the components.
May – This month, the water treatment plant, cooling water system, and switchboard were all officially finished and handed over from construction to the commissioning team. The ductwork lagging (insulation and cladding) also made excellent progress, and the expansion joints were installed. The steam piping was very near completion – to be closed out with a final pressure test in mid-June. The Commissioning team, made up of MGA Thermal engineers and our experienced consultants, had finalised all procedures and safety requirements to move the finished plant areas into the commissioning phase.
June – The construction of our demo unit was on the very cusp of completion! All plant areas, the water treatment, cooling water, steam system, and thermal energy storage systems were about to be officially handed over to the commissioning team. The handover process utilised a series of check sheets and reports to ensure that the completed work was to the required operational and safety standards. Commissioning of the water treatment plant and cooling water system commenced and was nearly complete. The commissioning team moved on to the careful job of checking the control on all of the actuated valves, sensors, instruments, and fan/pump motors in the main two process areas, the steam and the thermal energy storage systems.
-
July – We were excited to announce that construction was complete!
Steam generation infrastructure, which included the HRSG, steam and water equipment, was completed. The boiler and piping successfully passed the pressure test, which was witnessed by a boiler inspector. Commissioning of the water treatment plant and cooling water system was completed.
The commissioning team had checked the control on all of the actuated valves, sensors, instruments, and fan/pump motors in the main two process areas, the steam and the thermal energy storage systems.
The loading of the TES enclosure with MGA Blocks had commenced.
August – The loading of MGA Blocks was complete; all 3712 of them!
With construction complete and the MGA Blocks (TES material) loaded, we progressively moved from cold to hot commissioning of the full system. During this time, we successfully commissioned the nitrogen loop and progressed through 15% and 25% load tests of the full system.
September – During the month of September, MGA completed the final tuning of P&ID (process and instrumentation) controls and final adjustments to the Demonstration Unit. The Demo Unit also moved to 24/7 operation and was operating as expected and designed, including for steam production.
MGA Thermal graduated from Shell Gamechanger and gave multiple global industrial clients tours of the Demonstration Unit.
October – During this quarter, MGA continued low-temperature then high-temperature commissioning of the Demonstration Unit. Through the ramp-up in temperature ranges, the unit had been running 24/7 and operating as expected and designed, including for steam production.
Unfortunately, late on the 5th of October, as MGA ramped the unit to 100% of the operating design temperature, the unit began to overheat, going beyond the 700°C intended temperature limit. As part of this, shutdown protocols were initiated and emergency services notified.
No injuries occurred and all personnel were evacuated from the building. No damage beyond the unit occurred.
The unit had now cooled. MGA initiated a full investigation into the incident and ongoing impact, including appointing an independent party, embracing Root Cause Analysis (RCA).
MGA Thermal remained committed to moving our company forward, with investor support in place. The learnings would help accelerate the development of our Thermal Energy Storage (TES) system.
Our MGA technology remained a crucial piece of industrial decarbonisation and long-term energy storage solutions. We continued to work toward our vision of making 24/7 renewable energy a reality.
November – The unit had fully cooled down, and the clean-up and disposal of the impacted parts had commenced. The good news was that much of the equipment external to the TES enclosure was undamaged and passed functional testing, meaning we could work quickly to rectify the project.
The incident investigation and Root Cause Analysis (RCA) were ongoing during November.
During this month, we also conducted a visual inspection of all damaged external components and began preparing to rebuild the plant. We included lessons learnt from the first build and prepared to implement any necessary additional findings from the incident investigation.
December – The investigation into the incident and independent party Root Cause Analysis (RCA) were completed in December. During this time and throughout the whole incident, MGA made transparent communications to key stakeholders a priority. That included the MGA team, investors, collaborators, and our customers. We received encouraging feedback and support throughout this period, demonstrating our stakeholders' confidence in the MGA way forward and the market potential.
We applied learnings to prevent the recurrence of another overheat and continued to work to rectify the unit.
MGA conducted a high-priority design review on critical plant items, including improvements to the manufacturability of the TES enclosure. We then placed an order for the new enclosure, expected to be onsite in early Q2 2024.
-
In January, detailed planning for the rebuild project was undertaken. Now that we had the full picture of the impact of the overheat, we finalised the project plan and management strategy to rebuild and recommission the Demo Unit. We re-engaged our expert consultants to help facilitate the rebuild and placed more orders for equipment; specifically replacement heater elements and heater element tubes.
February – Led by our TES Manager, leadership completed a walk-through of the Demo Unit, confirming expectations of any superficial impacts to be ready for presentation when the project was complete.
With our planning finalised in January, we powered along. Knowing the new TES enclosure was due to arrive onsite in early Q2 2024, we locked in the supply and installation of the enclosure insulation for the same month. We also sought tenders for replacement thermocouples and other plant instruments impacted by the incident.
March – In March, we started preparing the site for the new TES enclosure. We progressed with preliminary electrical site works and received delivery of instruments and electrical cables. The heater elements and heater tubes had been shipped.
We had regular project meetings to ensure we were on track to deliver the rectified Demonstration Unit to our stakeholders' expectations.
April – By the end of April, we experienced a massive win with the successful cleanout and removal of the old enclosure, ductwork, and other equipment that wouldn’t be used in the recommissioning. We engaged a very experienced team of industrial cleanout personnel who safely and effectively removed the thermal storage, enclosure, and insulating material from the pilot’s site, paving the way for the new enclosure to be placed and the ductwork reinstated.
May – May kicked off with the delivery of our brand-new, freshly painted thermal storage enclosure from Varley. The installation of the internal insulation and subfloor to support the new blocks began immediately and was finished by the end of May.
In parallel with the insulation works, the electrical installation of new heater elements and instrument cables started, including the cable ladder and ductwork reinstallation.
June – Work continued! The electricians were on site, continuing to install heaters and instrument cables to their termination points. Duct installation had also progressed; each section underwent rigorous leak testing and proofing before the final install and acceptance test.
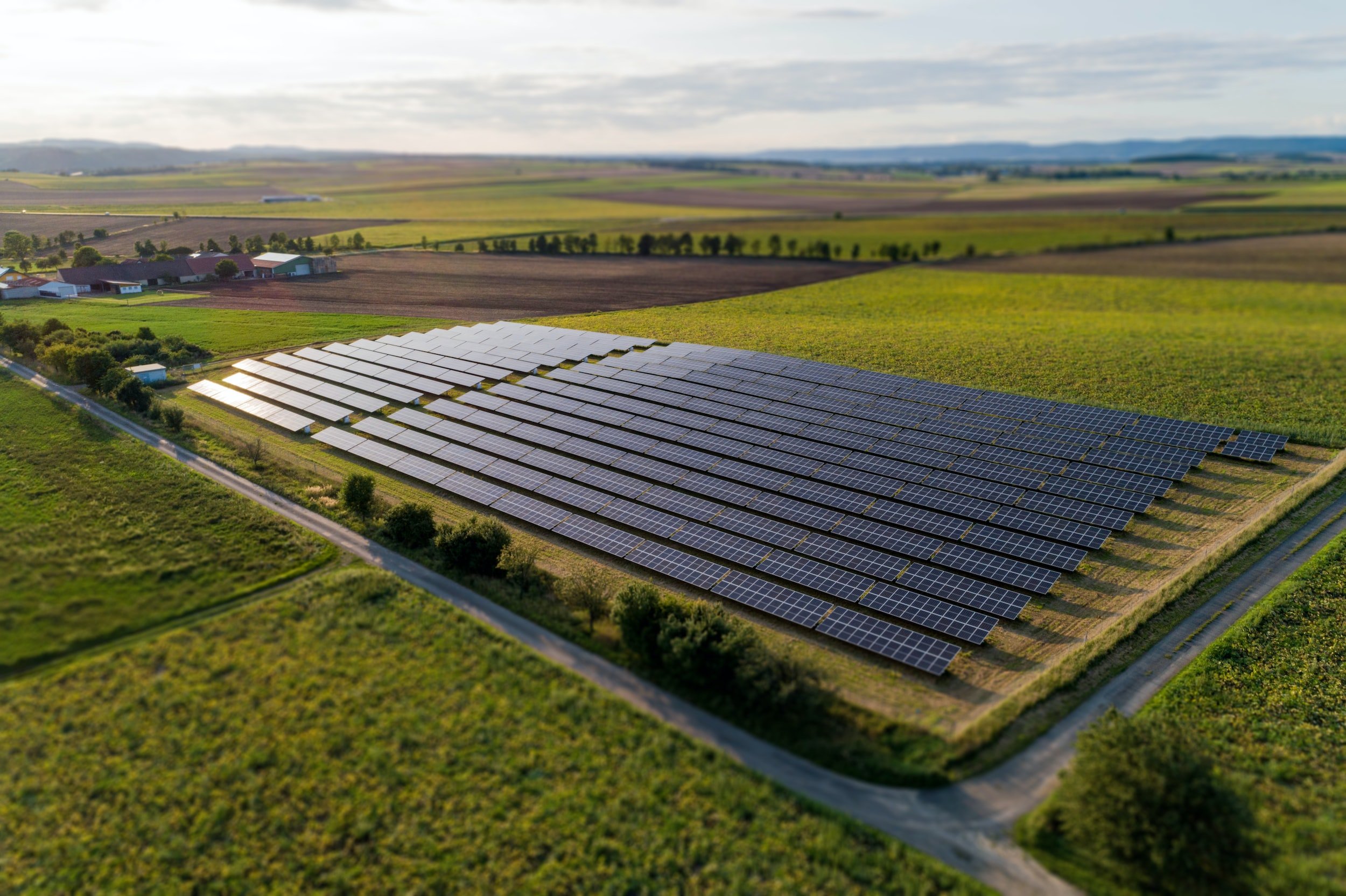
Industry Involvement
MGA Thermal are looking to actively engage with industry as part of this study. In conjunction with ARENA, we are forming a consortium of interested representatives - particularly those who are either generators of variable renewable energy or consumers of heat and/or power looking to decarbonise while maintaining a firm supply.
The consortium will help inform MGA Thermal of specific use cases to be demonstrated by the pilot and be kept up to date with progress and results.
If you are in one of the groups described above and interested in joining the consortium, please get in touch.
Note: The contents on this website do not belong to ARENA. To view ARENA’s project website, click here.
Stay up-to-date!
Subscribe now to our quarterly newsletter! We’ll also send you the big exciting updates about our demo Plant.